“Evolving the well-established”
Interview with Dr Martin Schneider
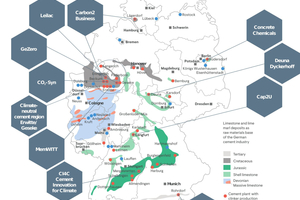
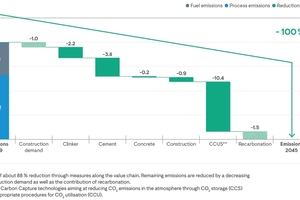
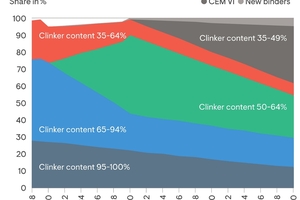
The 9th International VDZ Congress is just around the corner: From 6 to 8 November 2024 - for the first time since the COVID-19 pandemic - the VDZ Congress will provide a forum for global exchange in the cement industry. The focus in 2024 will be on key topics in cement process technology and the decarbonisation of the entire cement and concrete value chain.
In the following interview, Dr Martin Schneider, Chief Executive of VDZ, explains what the biggest challenges and bright spots in the industry are at the moment, what contribution VDZ‘s CO2 Roadmap will make to climate neutrality in the industry, and what key topics participants can look forward to at the 9th International VDZ Congress.
Dr Schneider, thank you very much for the invitation. What particular challenges is the cement industry currently facing?
Martin Schneider: The big issue, of course, is the transformation of the sector into a climate neutral industry. The cement and concrete industry worldwide is faced with the question of how to reduce CO2 emissions to net zero. As VDZ, we have been working for many years on the various paths that will ultimately form a complete roadmap for the decarbonisation of the industry. At the same time, we are involved in many projects around the world to help cement companies develop and implement their carbon reduction strategies. To be honest, in my many years working for the cement industry, I have never seen the sector so actively working towards a common goal. It‘s really good to see the industry wanting to be part of the solution, which is certainly very encouraging for all of us.
Do you have any examples of projects that are currently being initiated in this area?
Schneider: Firstly, the use of the classic levers that we know, the clinker-efficient cements. We now want to bring these to the market and, above all, ensure that they are purchased and that we can also use them appropriately in the concrete sector. We are making very good progress, especially in the area of CEM II/C cements.
The other lever is to further expand the use of alternative fuels, including biomass. This is a classic approach that we are trying to optimise further. While the substitution level is already quite high in some countries, the potential is greater in countries where less alternative fuels are used today.
However, the most important lever that needs to be applied to bring unavoidable emissions down to net zero is carbon capture. At VDZ, we have been actively working on this issue since 2007, together with ECRA, the European Cement Research Academy. A number of projects have already been initiated. In Europe, some of them are supported by the Innovation Fund.
As you can see, we need to work on the classic levers I mentioned earlier, but we also need to work on CO2 capture technologies. This is an important step for the sector, and we need to ensure that the boundary conditions that we cannot control on our own are also addressed at the political level. These issues are also the focus of our CO₂ Roadmap and our CO₂ Infrastructure Study.
The key question is how the industry can communicate the different elements of this transformation to the value chain and how CO2 efficient cement can be progressively integrated into the product portfolios of the cement industry’s customers.
Does VDZ receive support from politicians or are there certain political guidelines that support you in bringing green cement onto the market? How is the interaction between the politics and VDZ?
Schneider: Governments around the world are committed to reducing CO2 emissions. At the same time, they are among the largest users of cement. As a result, public procurement plays a key role in bringing CO2 efficient cements to the market. However, in most of today’s tenders, the price is of course the unique selling point. If the lowest price is on the table in a tender process, it will usually be accepted. The indicator of CO2 efficiency or the CO2 content of a product plays only a secondary role. The transformation to net zero will not only require efforts from manufacturers - the push effect - but also the pull effect from the market and our customers. This raises the question of what a green lead market actually is and how the carbon footprint of a cement is assessed. I recently took part in a conference organised by the German Federal Ministry for Economic Affairs and Climate Action (BMWK) to discuss how a project that has now been completed can be put into practice. The first step was to establish rules on what green cement is and how different levels of its carbon footprint can be assessed. There is a step-by-step model and different levels to work with. The whole value chain is working together on this.
You mentioned the infrastructure study above. Could you please summarise what tasks VDZ takes on in order to support the cement industry on the path to climate neutrality, but also in general?
Schneider: As VDZ, we have grown over many decades and our work is based on three pillars: Firstly, we represent the industry; secondly, we are active in research; and thirdly, we provide services for our customers. We have developed these pillars over many years and they are mutually beneficial. I believe that what we all have in common at VDZ is that we are deeply rooted in the cement industry. From our origins in 1877 to the present day, we have shared a passion for the cement industry and thus, of course, primarily for the member companies here in Germany, but also for the international cement community.
Based on our self-image, we think about where the industry is going, and perhaps we think ahead for the industry in some areas, especially in the area of decarbonisation. But we also think about what opportunities the industry has to develop in general. This raises issues such as what to do with CO2. Before each manufacturer thinks about who they need to talk to - the regional, state or federal government - we at VDZ make sure that communication on this issue is coordinated and also works at the political level.
In recent years, we have published several studies to actively support our industry on the path to climate neutrality. In order to decarbonise products and processes, completely new ways must be found in the production of cement and its use in concrete. Our CO2 roadmap published in 2020 shows how this can be achieved: using two decarbonisation pathways, the study analyses the CO₂ savings that can be achieved along the cement and concrete value chain by 2045 (https://vdz.info/cp). Due to the high proportion of unavoidable CO₂ emissions, there is no way around CO₂ capture. A suitable infrastructure for CO₂ transport is therefore also required for the subsequent storage or use of CO₂. Against this background, VDZ recently presented its 2024 study on “Requirements for a CO₂ infrastructure in Germany”. It shows the unavoidable CO₂ emissions to be expected from the three sectors (see https://vdz.info/co2i). Based on this, the study analyses how the demand for CO₂ transport will develop, how a CO₂ infrastructure should be designed, and what requirements it must meet to achieve climate neutrality.
Keyword pioneering role in climate neutrality: Let’s talk about the roadmap for CO2 neutrality. Could you briefly summarise the key messages of the roadmap?
Schneider: The aim is to have a net zero CO2 cement at the very end, so that we can develop, use or sell a net zero CO2 concrete. We have to look at what levers are available. There are the classic levers as mentioned above, which can perhaps be developed further, levers that are still being developed and, above all, levers that are cheaper than others. In our CO₂ roadmap we have considered which levers can contribute and how. At the end of the day, there will always be unavoidable CO2 emissions that need to be captured. And because this is a relatively expensive business - capture, transport and storage - we will do everything we can to keep the remaining emissions as low as possible. And that requires the industry to pull all the levers in the value chain as far as possible throughout the process and to produce the clinker as efficiently as possible.
We have seen, of course, that increasing thermal efficiency or using biomass, for example, are approaches that have been practised in many countries for years. Again, the question is: Can I get the last bit out of it, and how can I use the clinker in the cement as efficiently as possible? When you think about how to develop these approaches further, completely new ways of thinking come into play. Or look at cement and its use in concrete: a “one size fits all” solution is no longer needed. In the case of cement for indoor use, for example, since the concrete does not need to be frost-resistant, the clinker factor can be further reduced and new CO2 reduction potentials can be tapped. Furthermore, in order to use cement and concrete as efficiently as possible, the entire value chain can then consider which levers can be used at which point to keep the remaining amounts of CO2 as low as possible.
Does this also go hand in hand with the tenders that are issued for certain buildings?
Schneider: Green lead markets need to be tangible. The Price has always been the key element, but this is changing. The whole value chain is also showing an interest in being part of the overall solution, and the demand for sustainable products and green buildings will go hand in hand. This is important for us as an industry: for the first time we have an issue that we cannot solve alone, unlike traditional emission issues, for example. Today, we need not only equipment suppliers on our side to develop processes with us, but also customers who believe in sustainable products and are prepared to play their part. This requires external conditions such as sufficient renewable energy or a CO2 infrastructure. It‘s a whole new dimension.
Is CCU, or Carbon Capture and Utilisation, an issue and is this step worthwhile in terms of energy?
Schneider: Ultimately, CCU will play an important role. At the moment it is more obvious to go for storage, i.e. CCS, because it is more cost-effective. The reason for this is that renewable energy is precious and may first be needed for other purposes than CCU. But once a full value chain is in place, it would be unwise not to use CO2 as a feedstock. Nevertheless, there are regions where favourable conditions already exist today. If there is a concept for how it can be used in a concrete way, then CCU definitely makes sense. But as things stand today, CCS has priority for the time being.
You mentioned that the steps towards climate neutrality in the industry will lead to an extreme increase in cost factors. In your opinion, is this an issue that poses problems for small and medium-sized cement manufacturers in particular? Or are there perhaps already solutions that would allow everyone to take this step together?
Schneider: In fact, CO2 costs are already a significant part of our production costs. These costs will increase, but it won‘t make it impossible to build. After all, cement is part of the whole value chain; if you look at buildings, for example, the cost of cement is rather a minor issue. That doesn’t mean that there won‘t be price jumps in the value chain. But this has to be seen in the context that there is no alternative to climate neutrality. It will be important for the sector to have a level playing field between net zero cements and those with a larger CO2 footprint. On the one hand, the international market will be taken into account in which context Europe has introduced a Carbon Border Adjustment Mechanism. On the other hand, at a more national level, we have the problem that the investments - especially for carbon capture technology - are so huge that companies that are early adopters of carbon neutrality need to be supported in their investments. In Europe, the innovation fund helps; at the country level, additional measures such as carbon contracts for difference are important. So, there are opportunities for small and medium-sized enterprises. And the significant number of carbon capture projects underway around the world clearly shows that cement companies are making use of them.
To what extent has the cement industry already started implementing the goals from the roadmap?
Schneider: There are currently an incredible number of technical approvals for new cements, especially CEM II/C cements. Technical approvals are helpful because cement standardisation at European level is still on hold, it may take some time because the Construction Products Regulation has not really taken off yet. We also have many projects for CO2 capture. At VDZ, we have been working on this issue since 2007. Within ECRA, we have developed the oxyfuel kiln for this purpose. In 2018, a small industrial consortium that found itself in ECRA decided to build the kiln in Mergelstetten in southern Germany together with Polysius using this process.
Are there currently any other new concepts that will help the cement industry to remain fit for the future in the longer term and to move forward in a sustainable way?
Schneider: We face the huge challenge of producing 4.5 billion t of cement globally a year. And when we think about the future now, we always have to think about scalability. Of course, there are start-ups that already have ideas about what the cement of the future might look like, but we need to see how feasible these ideas are when it comes to their practical implementation. At first glance, it doesn’t look like some of them will ever get beyond the niche stage. This is not to say that there are no significant contributions to be made, but we can only produce the vast quantities of cement that are needed if we work with traditional raw materials. In order to obtain the necessary quantities of raw materials, we cannot resort to “exotic” minerals, but must use something that is readily and abundantly available in the earth crust. I believe that this is the case at the moment, and for me the most important part of tomorrow’s cements will still be Portland clinker. So the overall objective remains to use cement in concrete and concrete in construction as efficiently as possible in the long term, so that all components are used as effectively as possible.
VDZ’s claim is “Evolving the well-established”. In your opinion, where in the industry does this claim have the greatest impact?
Schneider: Much of our day-to-day business in the cement industry has a long tradition. At VDZ, too, we work with materials that have been improved over time, but have remained essentially unchanged for more than 200 years. So the question is, in view of the major challenges we face - climate protection, circularity - how can we look to the future with our products without losing sight of our tradition? At VDZ, we believe that our roots are the basis for the future development of our industry. This applies to our materials, i.e. we will continue to produce cement based on limestone and clay as raw materials. But at the same time, we are looking beyond what is known and feasible today. We are trying to lead our industry into the future, which will of course be different from today‘s perspective. But we see it as a great opportunity, because cement and concrete are materials that will be needed in the medium and long term. It is in our hands to shape the industry of tomorrow, in a decarbonised way, fully part of a circular economy and for the benefit of people.
Dr Schneider, you have been with VDZ since 1991. What are the most important insights you have gained during this time, both privately and professionally?
Schneider: I am a physicist by profession, and when I started at VDZ I knew nothing about cement and concrete. However, I soon found this material extremely interesting: firstly, from a scientific point of view, covering chemical, mineralogical, physical and process engineering aspects. At the same time, I felt that cement is such an important material for today’s world: Imagine what a world without concrete would be like? So I still have a lot of respect for cement and concrete and the important role it plays in our built environment and therefore in people‘s wellbeing.
Against this background, it was clear to me that it is a great responsibility, especially for an organisation like VDZ, to make cement and concrete as sustainable as possible. I was able to take on this responsibility personally and I am very happy to have been able to make my own contribution in this important field.
VDZ was and still is an excellent environment in which to develop. I have had the opportunity to work in various areas: environment, process, chemistry and finally, since 2000, as CEO. In this role I have been able to develop not only VDZ as an organisation, but more importantly, its people. I have a great team and we all share the values that we have developed over the years. These values are our compass, they give us strength and confidence, even - I should say especially - in difficult times. As you can see, I am a happy man with a great job and many reasons to be grateful.
Are there any other goals that you would like to achieve together with VDZ?
Schneider: The ultimate goal, of course, is to continue to support industry in its transformation. There is still a long way to go, but the first steps we have taken so far are very promising. Five years ago, I would not have thought this was possible.
When we started working on decarbonisation a few years ago, it was not clear where we would end up. But look where we are today: We are moving towards net-zero CO2, and I am confident that we will succeed. Of course, there are many challenges and we need the right framework conditions. Ultimately, however, I believe that the role of the VDZ is also to help find solutions to the many questions that still need to be answered. In this respect, I think that our role will also be to work together with the industry on the decarbonisation of the sector - which will, of course, also create confidence that this can be achieved. We will continue to work with equipment suppliers, but also with policy makers and of course with society in general. I think we should really think of cement as a binder in a broader sense, connecting people who are working towards a common goal for mutual benefit. And some of them do it with great passion.
Finally, let’s talk about the VDZ Congress 2024: What are the big topics that attendees can expect?
Schneider: The big issue, of course, is transformation, with all the elements I have mentioned. One focus will be on CO2 capture, because that is the topic that is being worked on at an extremely high level at the moment. We are also expecting speakers on CO2 transport and handling in particular, but also on industries or companies dealing with materials such as calcined clays or granulated blast-furnace slag. Of course, there will also be presentations on traditional process engineering, flue gas cleaning and grinding technology. But we will also be inviting plant manufacturers to present their concepts. We will also be thinking about new material developments, for example by involving start-ups.
Is the focus of the 9th international VDZ congress 2024 primarily global or is the content clearly focused on Germany or Europe?
Schneider: The VDZ Congress has a global focus; many speakers will come from Europe, but we also have great contributions from many other parts of the world.
In choosing the right topics, we always try to keep an eye on practical relevance and strike a balance between the tried and proven and new ideas. I believe that our roots in industry set us apart from purely academic approaches. We try to bring the best of both worlds to our industry and drive the transformation. This will also be reflected at the VDZ Congress. The main addressees are therefore the people in the cement industry, and the main objective is to ensure that they can derive the greatest possible benefit from this.
What will be the greatest added value that participants can take home with them?
Schneider: There are several aspects to this. Firstly, the aim is to provide participants with concrete, practical solutions. We at VDZ and our congress are known for approaching the speakers and not the other way around. There is no call for papers; instead, we decide which topics and speakers are suitable.
The second point is the sense of togetherness, which you can also feel because we are dealing with issues that are currently affecting the entire industry. Looking back, the issues presented at the congress should help all attendees to further develop their companies. The third major added value is pride in the progress of the industry. What are we working towards together? How are we doing compared to previous congresses? So the three main points are: technical expertise, shared progress and shared pride in what we have achieved. We are an industry with a history, a tradition and, of course, a future. We are an essential sector and our job is to be part of a bigger solution. These are all things that we live by at the congress and as VDZ.
As VDZ, are you in close contact with other associations in Europe, such as CEMBUREAU?
Schneider: We are in contact with CEMBUREAU, GCCA and the international cement associations and our cooperation is a great partnership based on friendship and mutual trust. We learn from each other and support each other, especially in the big area of decarbonisation.
Dr Schneider, thank you very much for the interesting interview and the many insights into current topics in the cement industry.
www.vdz-online.de/en/knowledge-base/events/international-vdz-congress-2024